EV には 800 V が必要、800 V にはシリコン カーバイドが必要
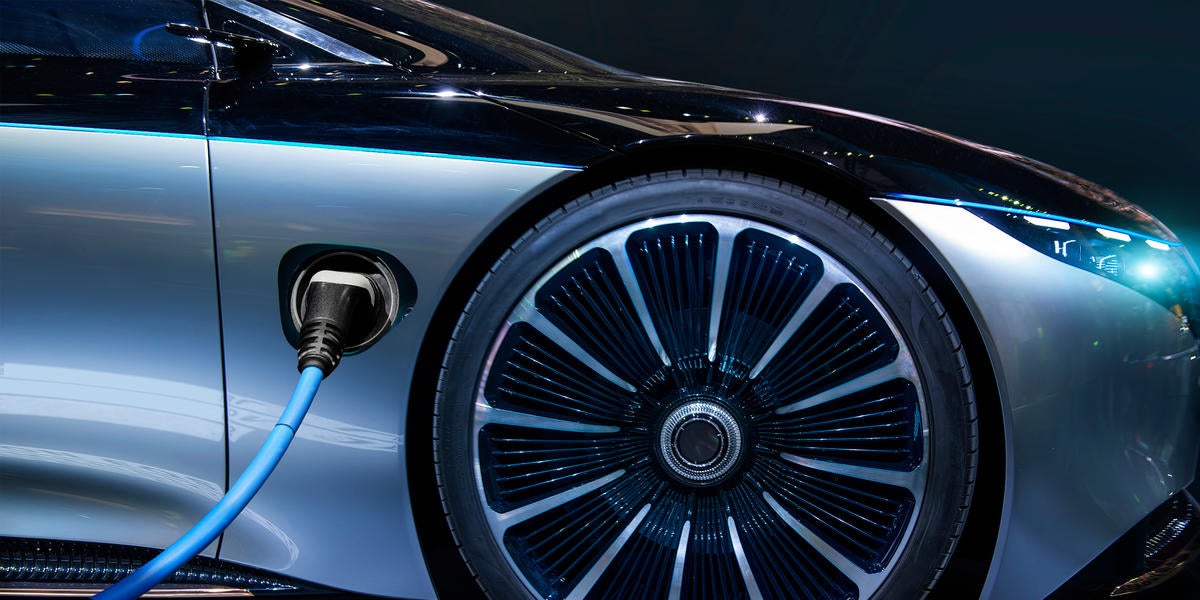
800 V の電気自動車 (EV) が登場し、その数は増え続けています。800 V システムは、ポルシェ タイカンやアウディ e-Tron GT などの高級 EV で始まり、その後ヒョンデ Ioniq5 や起亜 EV6 で主流となりました。ゼネラル モーターズとリヴィアンは、将来の EV を 800 V 対応にすると発表しています。[1] 他の企業もこれに続くと予想されています。
現在の 400 V ドライブ トレインの 2 倍に相当する 800 V の使用が可能になれば、大きな可能性がもたらされます。電圧が 2 倍になれば、充電時間を半分に短縮することができます。ヒョンデ Ioniq5 と起亜 EV6 は、200 kW を高速充電でき、10% から 80% までの充電を 18 分で行うことができます。ポルシェ タイカンは、5% から 80% まで 22.5 分で充電することができます。400 V で 100 kW に対応する充電ケーブルやコネクターは、800 V で 200 kW の出力が可能です。800 V 単体ではドライブ レンジが飛躍的に伸びるわけではありませんが、充電時間を大幅に短縮できるため、航続距離への不安が軽減されます。
また、電圧が 2 倍になると、同じ電力レベルであれば電流も半分になり、ケーブルのサイズと重量を減らすことができるため、EV が軽量化されます。低電流化により発熱を抑え、環境に優しい EV を実現します。高電圧化と巻線の小型化により、高電力密度で高効率のトラクション モーターを設計することができます。[2]
800 V EV にはシリコン カーバイド電力コンバータが必要
シリコン カーバイド (SiC) は、シリコン製のパワー MOSFET や IGBT に比べ、より高い性能を発揮することができます。SiC のバンドギャップが 3.26 eV であるのに対し、シリコンは約 1.12 eV であるため、SiC デバイスの高温でのリーク電流は小さくなります。
SiC はシリコン (0.3 MV/cm) に比べ、破壊臨界電界電圧が 2.8 MV/cm と高く、オン抵抗を大幅に低減させることができます。高ブレークダウン フィールドにより、SiC デバイスはシリコン デバイスよりも薄くなり、スイッチング損失の低減、通電能力の向上、高速スイッチングが可能になります。その結果、SiC MOSFET はシリコン MOSFET のような高周波スイッチングに対応しながら、IGBT に近い電流、電圧定格を実現し、EV 用電力コンバータとして非常にマッチしています。
SiC を用いた高周波スイッチングは、スイッチング速度の遅い IGBT を用いた設計と比較して、電力コンバータの大幅な小型化を実現します。
熱伝導率も、シリコンと比較して SiC が優れている部分です。SiC は熱伝導率が高いため、同じ消費電力であれば接合部温度 (Tj) の上昇が小さくなります。また、SiC MOSFET はシリコン デバイスよりも高いジャンクション温度を扱うことができます。SiC デバイスは 600℃ の最大ジャンクション温度 (Tj(max)) に耐えることができますが、市販のデバイスはパッケージの関係で 175 ~ 200℃ に制限されています。一方、シリコン デバイスは Tj(max) が 150˚C であるため、冷却の必要性が高まり、ソリューションのサイズが大きくなります。
800 V EV には SiC ベースの補助 DC-DC が必要
トラクション電源バスが 800 V になっても、EV の補助電源バスは DC 24 V または DC 48 V のままと予想されます。EV には、800 V から 24 V または 48 V の DC-DC コンバータを実装するための高集積、軽量、高効率の技術が必要です。
補助電源の設計者は、高電圧、AEC Q100 認定電源 IC である InnoSwitch3-AQ ファミリーを利用することができます。これらの IC は、1700 V の SiC MOSFET を内蔵し、絶縁が強化されています。部品点数を最大 50% 削減し、小型化と軽量化を実現しています。
これらの電源 IC は、全負荷範囲において最大 90% の効率を実現しています。無負荷時の消費電力は 15 mW 以下で、電気自動車のバッテリー マネージメント システムにおける自己放電を低減します。また、製造、組立、テスト サイトは、IATF16949 認定の自動車品質マネジメント システムを採用しています。
資料
[1] https://www.greencars.com/post/new-800-volt-fast-charging-systems