GaN이 가능한 곳엔 반드시 GaN을... 그리고 계속해서 확장되는 GaN의 가능성
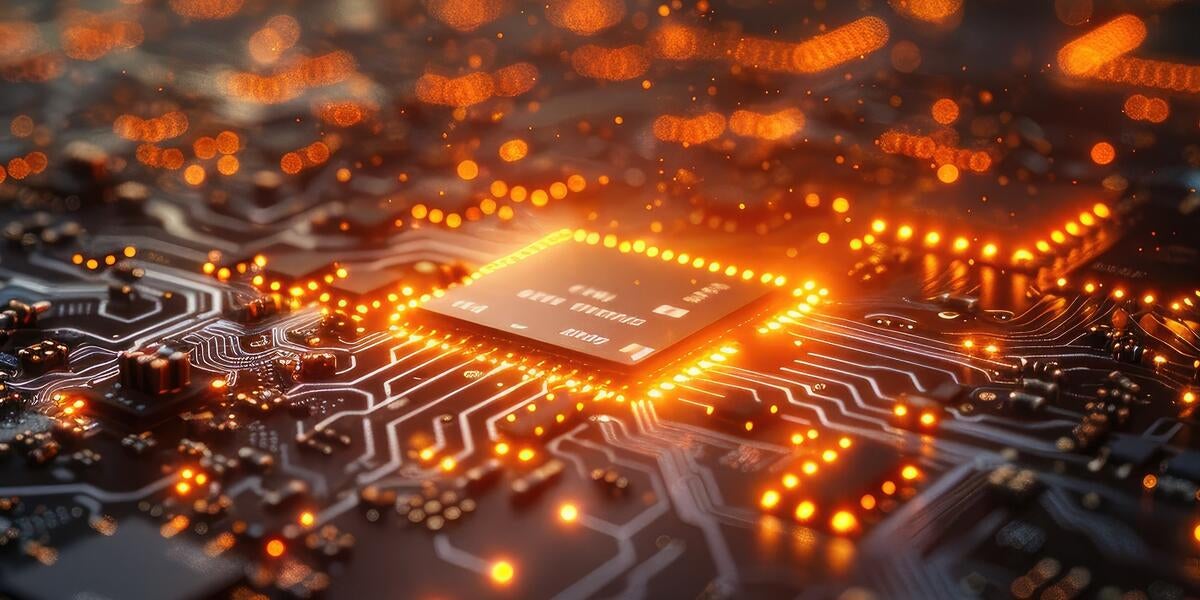
SiC, GaN, SJ MOSFET, IGBT 중 어느 것을 사용해야 할까요? 각각은 저마다 역할이 있으며, 그렇기 때문에 파워 인테그레이션스(Power Integrations)는 GaN을 하나의 시장이 아닌 하나의 기술로 간주합니다. GaN은 SiC와 다양한 MOSFET 기술과 함께 우리가 보유한 수많은 기술 중 하나일 뿐이며, 우리는 각 애플리케이션에 가장 적합하다고 판단되는 기술을 사용합니다.
최근 우리가 출시한 항복 전압이 1700V인 GaN 디바이스는 그야말로 극적인 성과였으며(이 표현은 충분히 타당하다고 생각합니다), 이를 통해 GaN 기술의 위상에 대한 인식이 크게 달라졌습니다. 좀 더 쉽게 설명하면, 1700V는 우리가 이전에 보유한 최고 사양보다 450V 더 높고, 다른 제조업체가 제공하는 최고 사양보다 70% 더 높은 수치입니다(참고로, 해당 경쟁 제품은 현재 대량 생산 가능한 수준이 아닌 것으로 알고 있습니다). 대부분의 GaN 업체들은 750V를 넘기기도 어려워하는 상황에서 우리는 1700V 정격의 플라이백 파워 서플라이 IC인 InnoMux™-2를 출시했고, 이 제품으로 1000VDC 철도 애플리케이션도 무리 없이 지원할 수 있습니다. 대량 주문 시 16주 납기로 배송 가능하며, 샘플은 즉시 출하 가능합니다.
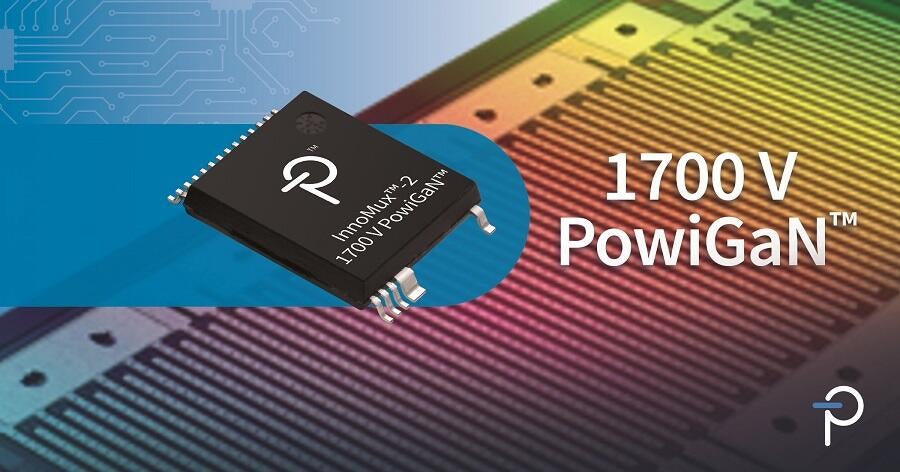
이것이 업계와 ‘GaN vs SiC, 어떤 파워 IC 기술이 더 우수한가’라는 논의에 가지는 의미는 무엇일까요?
간단히 말해, 우리는 GaN이 곧 수십 와트에서 수백 킬로와트에 이르는 모든 애플리케이션을 지원할 수 있을 것으로 믿습니다.
자세히 살펴보겠습니다. GaN은 이미 30W~240W의 저전력 충전기 시장을 석권했습니다. 슈퍼 정션 MOSFET보다 훨씬 효율적이며, 스위칭 손실이 거의 없고, 특정 RDSON이 매우 낮기 때문입니다. 따라서 더 높은 전력 밀도를 구현할 수 있고, 디바이스를 더 작거나 더 강력하게 만들 수 있으며, 열 관리 문제도 크게 줄어듭니다. 또한, MOSFET은 현재 GaN HEMT보다 저렴하지만, 고급 공진 토폴로지와 히트싱크가 필요하기 때문에 시스템 수준에서는 GaN보다 비용 효율성이 떨어집니다. 이러한 GaN의 이점은 생산 규모가 커지고, 생산량이 증가할수록 더욱 커질 것입니다. MOSFET이 초저전력 애플리케이션(예: <20W)에 선호되는 유일한 이유는 저전력 레벨에서 GaN 칩이 매우 작아 다루기 어렵기 때문입니다.
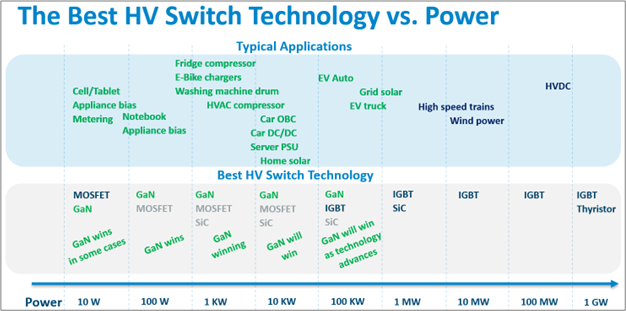
전력 수준이 500W, 1kW, 10kW까지 높아지면서도 GaN은 여전히 우위를 점하고 있습니다. 여기서 다루는 애플리케이션은 냉장고, 전기 자전거 충전기, 세탁기와 같은 백색 가전, HVAC 컴프레서, 태양광, 자동차의 온보드 충전기 및 납축전지 교체 회로, 서버 PSU 등입니다. 이 모든 애플리케이션이 MOSFET에서 전환되고 있습니다. 일부는 이미 SiC로 전환했고 SiC와 GaN은 효율 등급이 비슷한데도 왜 여기서는 GaN이 우세할까요? 간단히 말해서, 비용 때문입니다. SiC는 필요한 높은 공정 온도를 생성하기 위해 엄청난 양의 에너지가 필요하지만, GaN은 그렇지 않습니다. GaN 디바이스는 본질적으로 실리콘 부품보다 비싸지 않으며, 같은 생산 라인에서 상대적으로 조금만 수정하고도 제조할 수 있습니다.
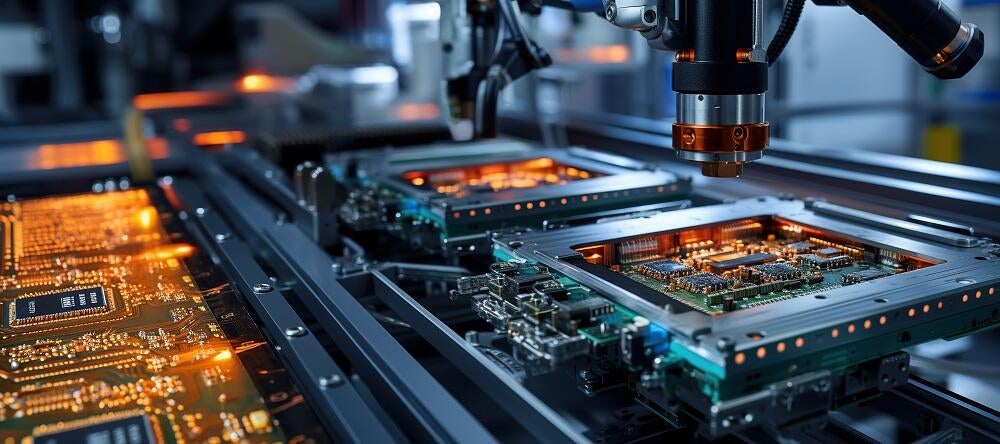
이전에는 MOSFET과 SiC가 담당했던 1~10kW 애플리케이션이 점점 더 GaN으로 구현 가능한 영역이 되어가고 있으며, 이와 같은 변화는 앞으로도 계속될 것입니다. 현재 GaN의 최대 출력은 약 7~10kW입니다. 이는 전기차 인버터 시장, 즉 가장 큰 파워 IC 애플리케이션 TAM의 요구를 충족하기에는 다소 부족하지만, 10배만 더 추가하면 수백 kW 수준의 전기차 전력 수준에 도달할 수 있으며, 첨단 기술 분야에서 10배까지 전력을 높이는 것은 불과 몇 년이면 가능합니다. 실질적인 제약이나 물리적인 한계는 없습니다. 필요한 것은 발명이나 영감이 아닌, 개발입니다.
수 메가와트급 풍력 터빈이나 기가와트급 고전압 DC 설비와 같은 초고출력 영역에서는 IGBT가 이미 널리 사용되고 있으며 비교적 저렴합니다. 따라서 SiC는 수직 구조 기술이 제공할 수 있는 고전류를 필요로 하는 시장의 비교적 작은 부분에 집중될 것으로 보입니다.
마지막으로 한 가지 더 말씀드리겠습니다. 새로운 기술이 등장하거나 중요한 진전을 이루면, 가장 먼저 그 기술은 기존 기술을 직접 대체합니다. 그러나 이후에 통찰력 있는 누군가가 등장해 말합니다. “그 방식도 괜찮지만, 새로운 기술을 통해 기존 설계를 완전히 재고할 수 있다. 기존 기술의 요건을 다시 고려하지 않고도 새로운 기술을 최대한 활용하는 새로운 컨셉을 생각해 낼 수 있다.” 우리는 마이크로 전자기술, 패키징, 시스템, 알고리즘 수준에서 혁신을 거듭하여 효율, 비용 효율성, 부품 수에서 획기적인 애플리케이션별 전력 제품을 개발하고 있고, 새로운 시장을 여는 새로운 아이디어를 창출하고 있습니다.
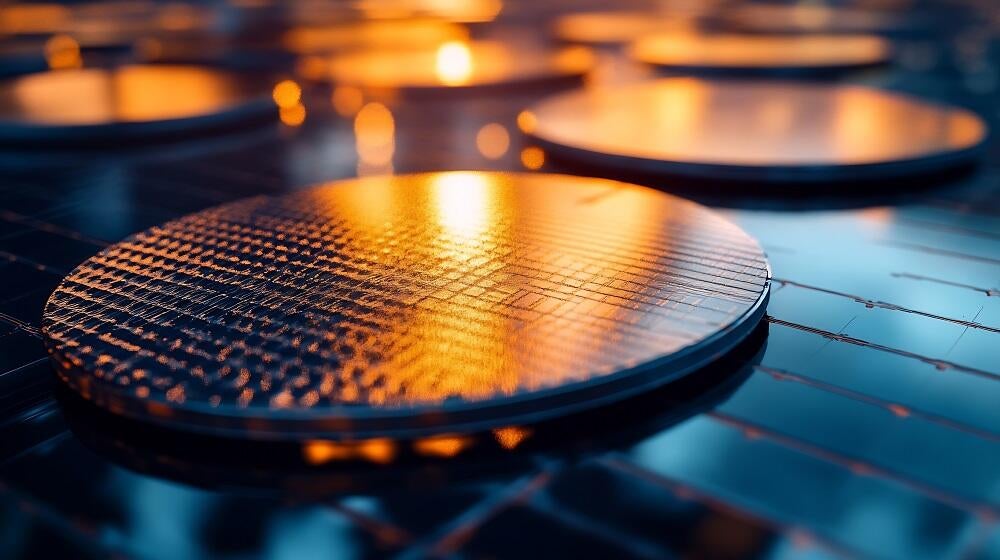